Petrochemical and Refining
Analytical Solutions for Petrochemical & Refining
ANALYTICAL SOLUTIONS for Petrochemical APPLICATIONS
Innovative Instrumentation, Gas Analysis and Process Control Solutions for the Petrochemical and Refining Industries
Process Insights is your SINGLE SOURCE for complete flare gas analysis for total compliance – Quad O, HON, MON and EMACT, RSR, Subpart Ja, HRVOC and more.
Petrochemicals find application in a wide range of products, spanning from clothing to electrical appliances. Within the Petrochemical Industry, there is a diverse array of applications that require monitoring of substances like Ethane, Propane, Ethylene, Polyethylene, Ethylene Oxide, Chloride, Carbon Monoxide, and more. The exploration of alternative methods to enhance the production processes, specifically involving ammonia, ethylene, and ethylene oxide, is of utmost importance.
Operating in the petrochemical industry involves the handling and processing of hazardous gases, which can present significant safety hazards if not monitored diligently. By utilizing gas analyzers, operators can identify and measure the presence of toxic, flammable, or explosive gases in the environment, enabling them to implement appropriate safety precautions to avert accidents and safeguard personnel.
The EPA introduced the new Emissions Guidelines in December 2023, outlining procedures for states to formulate plans to restrict methane emissions from existing sources. Acknowledging the critical role of oil and natural gas operations as the most significant industrial source of methane pollution in the U.S., this initiative represents a pivotal step toward a cleaner and more sustainable future. Read the new EPA guidelines regarding Quad O https://ow.ly/YG1850QguNJ
We know midstream applications. We will work to match your needs and budget and provide the optimal, and most stable process analysis solution for your application. We’re here to help.
WE’RE HERE FOR YOU
Get the most reliable, most precise gas analysis technologies available on the market today. We will work to match your needs and budget and provide the optimal, and most stable process analysis solution for your application.
For a complete range of analytical instrumentation, applications, systems, and service options, we will work to match your needs and budget and provide the optimal, and most stable process analysis solution for your application
APPLICATION SUPPORT
Allow our Support Team, consisting of Factory Trained and Certified professionals, to assess your application and specific requirements. We acknowledge that external conditions can lead to changes in your process parameters, necessitating the addition of components to an existing stream or the incorporation of a new stream. In response to this, we provide a wide range of cost-effective turnkey solutions that deliver exceptional performance, catering to your unique application needs. Explore our Application Support.
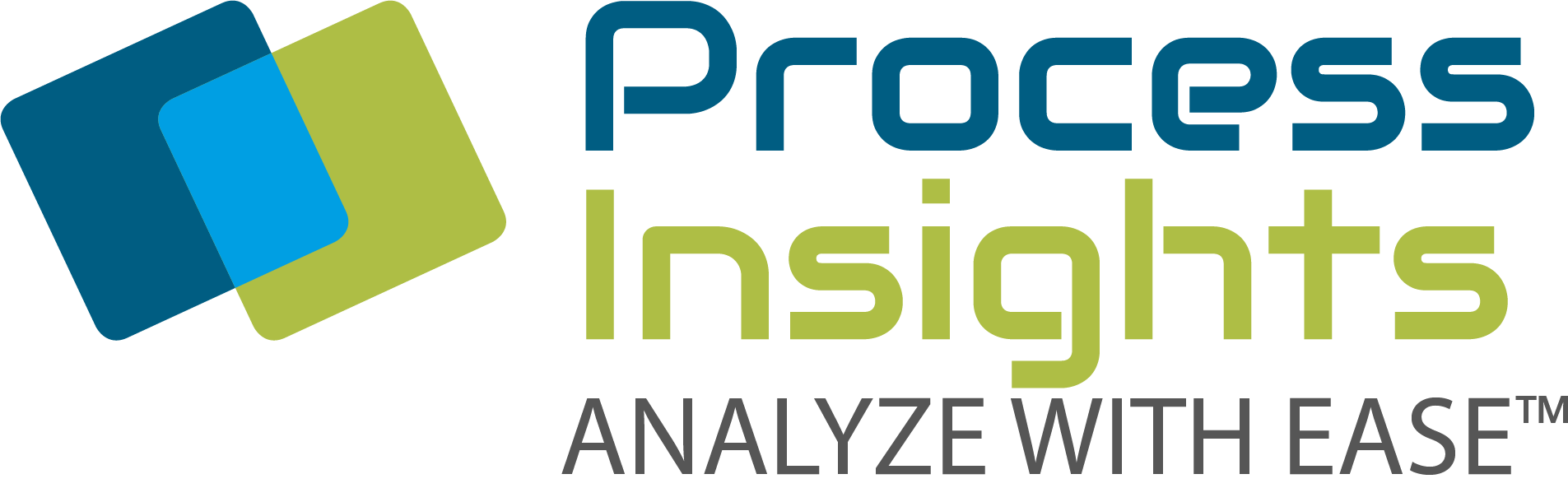
SALES | TRAINING INQUIRIES
AMERICAS: info.americas@process-insights.com
EMEAI (includes India): info.emeai@process-insights.com
APAC: info.apac@process-insights.com
CHINA: info.cn@process-insights.com
FEATURED PRODUCTS
ATOM INSTRUMENT™ TRACE-1000 S/N™ Analyzer
Our ATOM INSTRUMENT™ Trace-1000 S/N™ online process analyzer offers unmatched flexibility—configure it for trace sulfur, trace nitrogen, or both simultaneously! Featuring patented Excimer UV Fluorescence (EUVF) for sulfur and optimized chemiluminescence for nitrogen, it delivers precise measurements across diverse hydrocarbon process streams.
QuickTOCeco™ Water Analyzer
- Versatile for industrial applications in water treatment plants, industrial processes, environmental monitoring, drinking water quality control, pharmaceutical and biotechnology, food and beverage industry, and power generation
- Exact determination of TC, TOC, NPOC (Non-Purgeable Organic Carbon)
QuickTOCuv™ Water Analyzer
- Versatile for industrial applications for pure water, boiler feed water, condensate return, drinking water, surface water, and wastewater
- Continuous online determination of true TOC (detection of NPOC and POC/VOC), CODS, BOD, TC
- Certified housing for EX zones (EX p) (options for IECEx, etc.) Explosion protection Class I, Division 2, Zone 2 Groups ABCD
- Temperature Class: T4
TIGER OPTICS™ T-I Max EtO™ Trace Ethylene Oxide Gas Analyzer
Ideal for Chemical and Petrochemical Industries
- Offers rapid, continuous measurements with no calibration requirements or consumables.
• Meets the critically low detection limits necessary for updated NESHAP requirements.
• Ideal for facility-wide exposure monitoring and inventorying leaks. - Monitoring production and handling of ethylene oxide in chemical manufacturing plants.
- Preventing leaks and ensuring safety in storage and transport of EtO.
FEATURED PRODUCT
EXTREL™ MAX300-TGM™
Real-Time Toxic Gas Monitoring Solution in Ambient Air
Our NEW EXTREL™ MAX300-TGM™ Toxic Gas Monitor is a real time monitoring solution with analysis speeds of 0.4 seconds per chemical and gas clearing times of less than 3 seconds. These impressive speeds exceed industry requirements for continuous monitoring. With the ability to analyze 15+ chemicals per sample point, the MAX300-TGM toxic gas analyzer provides maximum efficiency at an extremely low cost-per-chemical, per sample point.
MAX300-TGM Advantages Include:
- Versatile and flexible analyzer – detect multiple chemicals on up to 46 sample points
- Fast measurement with high sensitivity, reducing false alarms
- Highly responsive to changes in chemical concentration – reducing down time after an event
- Streamlined operation – centralized analyzer for full facility monitoring
- Low cost of ownership and streamlined operation – decreasing complexity in maintenance and upkeep
- Industry leading application expertise and technical support with decades of experience with ambient air monitoring
- Large, user-friendly touch screen interface for at-a-glance updates with customizable alarm verifications