Calorimeters
Optimize Combustion with Accurate Calorimeter Measurements
Unlock Efficiency in Fuel and Flare Gas Applications
Plant operators seek swift and dependable measuring solutions for fuel gas and flare gas combustion, allowing precise control of the air/fuel ratio to minimize disruptions and maximize combustion process efficiency. In the USA, there’s no need to wait months for delivery. Reach out to our Calorimeter Experts today and experience delivery within just 4-8 weeks.
Our portfolio of Calorimeters, measuring Heating Value, Wobbe Index, Specific Gravity, and CARI, provides tangible value and assurance for compliance. With our cutting-edge solutions, achieve peace of mind while ensuring accurate and reliable measurements in your operations.
We offer two types of calorimeters
- “Injection-style” zero-hydrocarbon emissions calorimeters: Used for environmental monitoring of flares to meet the new and existing rules and regulations in refineries, chemical production facilities and mid-stream gathering plants. Handling high sulfur sample streams that plug other residual calorimeters.
- Continuous measurement calorimeters: Used in industrial and commercial settings, such as power plants, refineries, and chemical production facilities and mid-stream gathering, to monitor the energy content of the materials being processed and optimize the efficiency of the production process. By continuously measuring the calorific value of the material, operators can adjust the process parameters in real-time to minimize energy consumption, reduce waste, and improve product quality.
INDUSTRIES
Some of the industries that use our calorimeters include:
- Natural Gas: Used in the natural gas industry to measure the heating value of natural gas for billing and quality control purposes.
- Refineries: Used in refineries to measure the calorific value of fuels and feedstocks for process control and optimization.
- Power Generation: Used in the power generation industry to measure the heating value of hydrocarbon fuels and Hydrogen used in boilers and turbines. and other fuels.
- Biogas: Used in the biogas industry to measure the heating value of biogas produced from organic waste.
- Chemicals: Used in the chemicals industry to measure the calorific value of fuels and feedstocks used in chemical processes.
- Oil and Gas: Used in the oil and gas industry for measuring the heating value of natural gas, propane, butane, and other fuels.
- Petrochemical: Used for measuring the calorific value of different hydrocarbon feedstocks such as Methane, Ethane, Ethylene, etc.
- Environmental: Used in the Refinery, Chemical and Midstream industry to monitor flares.
- Co-Generation: Used to measure the heating value of high value waste hydrocarbon gases for the use in boilers and turbines.
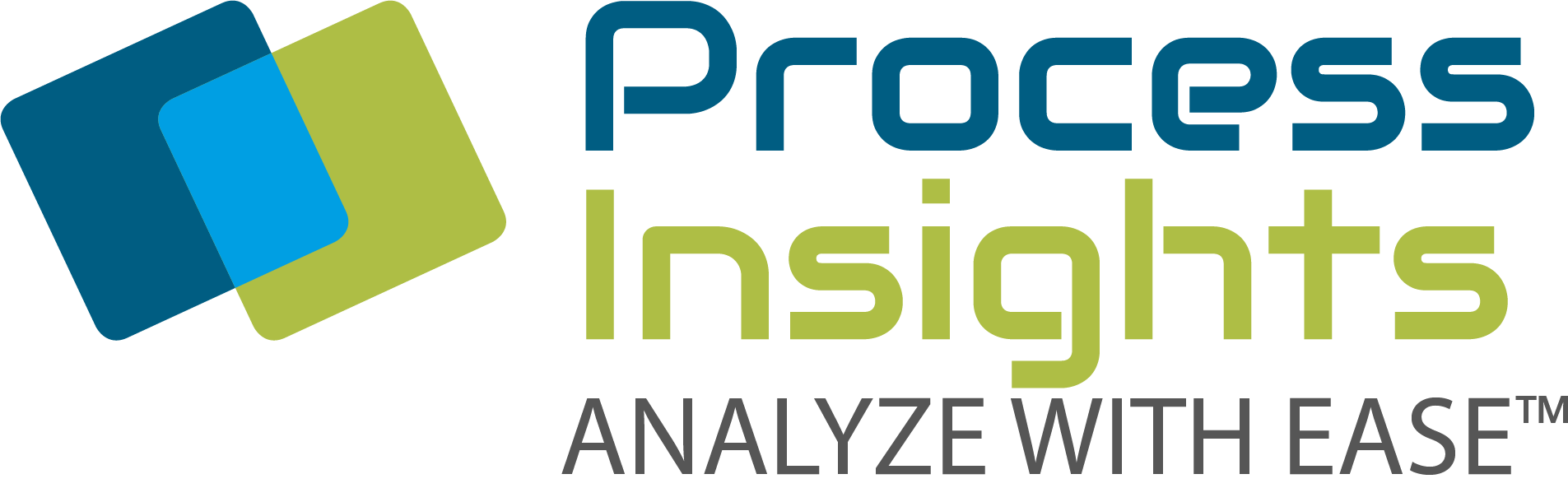

SALES | TRAINING INQUIRIES
AMERICAS: info.americas@process-insights.com
EMEAI (includes India): info.emeai@process-insights.com
APAC: info.apac@process-insights.com
CHINA: info.cn@process-insights.com